With the population in Omaha and surrounding areas continuing to grow at an increasing rate, the commercial landscape of Omaha is steadily changing and expanding as well. Omaha consistently has one of the lowest unemployment rates in the country. Because of this, new professionals are easily attracted to the area. All of this means good things for the construction industry, including a wealth of opportunities for exciting new projects and development.
The construction industry plays an important role in the economy. When the economy begins to slow down, the construction industry often feels the effects first – but when there is a strong demand for new construction, it’s an indicator the economy is on the right path. Despite the challenges presented by the pandemic, such as skyrocketing prices on building materials, major supply chain issues, and labor shortages, the construction industry persevered. According to the US Census, it is estimated that total put-in-place for 2022 was around $1.79 trillion, an increase of 10.2% from the previous year (construction put-in-place is the estimated total dollar value of construction work done in the United States).
Research indicates that the most pervasive trends in commercial construction in 2023 include increased use of biological construction materials, safety features, remote technology, modular construction, artificial intelligence, 3-D printing, design technology, supply-chain alternatives, and a move away from purchasing new equipment and instead renting or buying previously used implements. As we talked to local companies in the commercial construction business, we found some of the most common trends in the industry now include aerial imaging, attention to safety, quality, technology, and environmental impact, prefabricated construction with precision engineering and consistent quality; repurposing of existing buildings, sustainability, advancement in energy-saving designs, and more.
Are you ready to start from scratch with a new office building? Maybe you aren’t prepared to build a new office, but are interested in renovating an existing building. Regardless of the route you want to take, Omaha has many knowledgeable and experienced contractors that can help you create the most efficient and effective workplace.
Built on Trust
Huffman Engineering, Inc. (HEI) is a full-service engineering firm specializing in control system integration. From a commercial construction perspective, they work with manufacturing plants, industrial automation, and utility systems. You’ll find HEI programming automated controls for water and wastewater facilities or electrical utilities, working in pharmaceutical and life science plants helping to make human and animal medicine and vaccines, working with food and beverage companies, and material handling companies running everything from batch systems to create products to packaging systems to prepare them to be sold. Huffman Engineering is certified in several software and hardware applications, so they are often called on to bridge the gap between companies’ Information Technology (IT) and Operational Technology (OT) departments. Huffman helps with cyber security, data analytics, IIoT, and effectively are the brains behind systems that do great things in our community that most people never think about. In short, their tag line is ‘Making Ideas Work.’ They take a company’s ideas of how to make something faster, more productive, safer, stronger, or more efficient. Specifically, Huffman can integrate systems in different industries to help them make better business decisions.
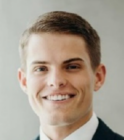
Dustin Bredvick
Huffman Engineering
“Huffman Engineering as a company works in a variety of industries so we have the benefit of really seeing the landscape of what is happening across the state in manufacturing and utilities. One thing that we are seeing pretty consistently is the need for upgrading older equipment that is nearing the end of its life cycle. A new facility within a pharmaceutical plant that produces animal medicine and vaccines reduced the likelihood of downtime after they replaced 22-yearold hardware that was no longer supported,” Mechanical Engineer Dustin Bredvick shared. “When a company gets to that point where they have to fish for replacements on eBay or scour the internet for used parts, that is a dangerous place to be. Not only will you likely pay higher rates to get the parts, but the likelihood that they will be damaged or not work as intended is very high.”
Similarly, HEI has recently been a part of upgrading some water and wastewater systems in communities across the State of Nebraska allowing these communities to secure these systems for the people in the communities for decades to come. When they can be a part of these lasting changes to fundamental systems that help communities thrive, Huffman knows they are truly engineering with impact.
“Critical manufacturing is in high demand right now. Upgrading water systems, food and medicine manufacturing, and electrical and natural gas utilities. We are looking at infrastructure in our country right now and the foundational systems we operate on and those that will take us into the future through manufacturing and developing new products are a focus,” explained Dustin. “At the same time we’re experiencing a labor shortage so automation is a focus. With a generation of skilled manufacturers preparing to retire and fewer and fewer employees trained in manufacturing, companies are looking to automation solutions and system integrators who know how to incorporate automation solutions into their existing processes.”
Through any kind of work being done, Dustin guaranteed that one thing stays the most important part of any project.
“For sure safety. This includes electrical safety, physical safety, and machine guarding. Robotics and automation require a level of safety and security including protection against cyber-attacks. With increased regulation in accordance with the FDA, USDA, EPA, and other regulatory agencies, compliance and knowledge surrounding updated regulations is imperative,” said Dustin. “Sustainability is also a hot topic these days as we all find ways to have some corporate responsibility for the ways we operate in the larger world. Specifically in the pharmaceutical world, clean environments are especially important down to what grade of polymer is required for a building that may need to be heated to 140 degrees Fahrenheit. As we work on specific projects with different variables depending on the industry and their regulations, knowledge of those specific regulations and the ability to validate our processes and prove quality checks becomes a hugely important variable.”
Companies planning for the future and setting themselves up for success in the marketplace are planning to upgrade equipment today and preparing for tomorrow. They are setting systems up to run for the next 20 years instead of hoping they can stretch for the next couple of years. By moving to new systems, they are mitigating risk, providing additional safety to operators and systems, often finding efficiencies, and setting themselves up for long-term success.
Recycled and Reclaimed
Once your building is built, it’s up to you to make it look its best. If you are looking for unique, aesthetically pleasing building improvement products, Out of the Box is the place to go.
Founded in 2011 by Jody Strauch and Steen Lundberg, Out of the Box offers the finest designer names in gently used recycled and reclaimed improvement products at affordable prices. Every piece in the 20,000-square-foot showroom has been personally selected for its exceptional quality.
Jody and Steen believe beautiful pieces deserve to be treated to the utmost in care: cleaned, tested, and displayed properly in a vignette setting in a well-lit showroom floor. Wouldn’t it be wonderful to be able to find that fabulous one-of-akind piece and clearly imagine how it would look in your office?
They feature the best in custom doors, lighting, furniture, entire kitchens and baths, all originally curated by top interior designers. Since these items are reclaimed or recycled, they are able to offer them at highly reduced prices!
Out of the Box is an environmentally green company and they strongly believe this is the way of the future – reusing remarkable products for a major renovation or simply selecting that special character piece for your home or office.
High-Quality Workmanship
Kingery Construction offers full service from pre-construction through the completion of the project. It is their mission to provide a superior level of professionalism, integrity, and honesty while offering cost-effective solutions in a timely manner. With exceptional management skills and a solid work ethic, the Kingery team can ensure that the highest-quality workmanship is evident on every project. They value their relationships and vow to remain true to their employees, project owners, vendors, and partners. Kingery has completed projects through a variety of processes including Design Build, Design Bid Build, Construction Management, and as General Contractor.
Kingery is proud to have recently completed Lincoln’s newest elementary school in the Waterford Estates neighborhood as well as eight years of improvements and new spaces at NECC in Norfolk. They are also currently in the third and final phase at Lincoln Regional Center ensuring safer spaces for patients. The building process has recently begun for the new Uehling Fire Station proving the perfect space for an extremely important volunteer fire department. The Omaha Kingery team is currently
working on several projects including Ralston High School, Mockingbird Community Center, and D.B. Property/ Voss Electric.
In recent years, the drive for environmentally friendly products and projects has increased. Many consumers are beginning to prioritize companies that use these eco-friendly processes, even at a slightly larger cost.
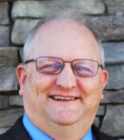
Rick Wintermute
Kingery Construction
“Green materials are still in high demand. In some projects where owners desire to be more eco-friendly, we have found many of the materials to be minimally more expensive options than normal building materials,” shared Rick Wintermute, Kingery vice president. “As construction costs, material supply, and workforce challenges continue to be a concern, we at Kingery have the experience and ability to assess the building project and find cost-effective alternatives to ensure the project isn’t affected negatively.”
In addition to getting eco-friendly, there are a number of other trends in commercial construction that Kingery has been adapting to and keeping up with.
“We are continuing to see a demand for warehouse and manufacturing spaces. This increase has prompted us to expand our Metal Building division which allows us the opportunity to bring the best construction options to our clients’ projects,” Rick explained. “There has been an increase in technologically integrated data with all systems in the building; heating/air, lighting, security, and access control.”
In January, Kingery Construction acquired Construct Inc. in Omaha. Construct Inc. fits into Kingery Construction’s strategy of providing excellent commercial construction services to the communities of Nebraska. The additional expertise and knowledge the employees in Omaha possess will ensure that Kingery Construction remains a top-notch provider of construction services for years to come.
Solutions for the Built Environment
AOI provides solutions for the built environment through their construction, furniture, and prefabricated construction divisions. With almost 40 years of service, their general contracting team successfully assists clients on single projects or with on-going construction needs, including new facilities, major remodels, conversions and additions, to minor repairs and renovations.
The furniture team can transform ordinary spaces into collaborative, innovative environments. They utilize the most credible and latest data to help their sales and design teams provide the necessary expertise to help clients create inspiring interior landscapes. As Nebraska’s MillerKnoll Certified Dealer, AOI offers the most comprehensive set of design brands in the industry. Each of these brands is uniquely innovative and together they add up to a robust portfolio of products that suit any company’s diverse needs.
AOI’s Prefabricated Construction team offers state-of-theart industrialized construction including interior walls, doors, power, technology, plant walls, timber, and casework from DIRTT Environmental Solutions. As Nebraska’s Certified DIRTT Partner, they’re leading a regional revolution of the construction process.
Prefabricated Construction has the ability to completely transform how construction projects are designed, priced, and delivered in the marketplace. DIRTT Environmental Solutions can take most of the typical processes of a construction project off-site, meaning that interior walls are prebuilt including doors, hardware, plug-and-play power, data and technology, glass and graphics, and more. When all interior walls, doors, power, and casework can be manufactured utilizing the accuracy and efficiencies associated with factory-built, industrialized construction, the balance of the project is generally completed more quickly, cleanly, and safely. This also takes pressure off of local labor markets that are already stretched to capacity. One of the primary benefits of DIRTT Walls is the flexibility of the finished environment. This means that any DIRTT interior environment is essentially future-proof.
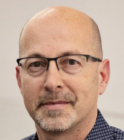
Marco Lade
AOI
“Prefabricated Construction is gaining significantly in popularity for workplace, education, and public sector markets with the largest gains occurring in health care. Owners everywhere are looking for reliability in their projects; reliability of design intent, price, and schedule. No construction methodology can currently deliver on all of these promises like Prefabricated Construction. We’ve completed some high-profile projects regionally using DIRTT Environmental Solutions that we’re very proud of including the new Lincoln Electric System Operations Center. This project included DIRTT walls, doors, power, and embedded technology,” Director Client Experience Marco Lade shared. “We also completed the Kiewit Omaha HQ project, a seven-story, 180,000-square-foot steel-framed building designed to foster collaboration and interaction. We provided DIRTT walls for all interior offices, meeting and conference rooms, including modular power on all floors. This project also utilized DIRTT Leaf Wall, DIRTT Breathe, and DIRTT Timber for interior collaborative and office locations.”
AOI is able to provide quick and reliable service with DIRTT Environmental Solutions that has proven to thrive even through difficult obstacles.
“The recent supply chain challenges in construction provided great opportunities for DIRTT Environmental Solutions to shine the light on several critical value propositions available to our clients including speed to market, fit and finish, and future flexibility,” explained Marco. “The standard lead times for DIRTT products are astonishingly short. Walls with power are 14 days manufacturing from order entry. Casework manufacturing is 21 days from order entry, while Timber is just 28 manufacturing days from order entry. The final interiors of a DIRTT project are almost always significantly higher in quality in fit and finish. More of your construction budget stays in your project on a DIRTT job.”
Always Meeting Your Needs
As a 100% employee-owned firm, you can be assured that Cheever Construction will deliver on their promises. The full-service general contractor/construction manager provides preconstruction services, construction management, and general contracting. Cheever Construction’s employees are invested partners that provide solutions for their clients. It is through these employee-owners that Cheever Construction is able to continue to perpetuate the principles of its founder and stay committed to a business philosophy that is dedicated to trusting relationships, excellence in performing services, workmanship that has enduring character and meeting clients’ expectations on every project.
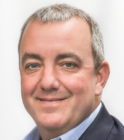
Justin Kurtzer
Cheever Construction
“Cheever is a relationship-based firm,” said President Justin Kurtzer. “We take pride in building trust with our clients and project partners in all that we do. We have built our reputation on our ingenuity, expertise, and exceptional people. We utilize an effective schedule, coupled with the quality and skill from our subcontractors and combined with our field craftsmen. Cheever Construction takes pride in all of the relationships that we have entered. We strive to make each project the precursor to the next project, while building a lasting relationship with everyone involved.”
In terms of commercial construction projects, Cheever Construction has seen high demand throughout all sectors of the industry, including retail, manufacturing, education, and medical. However, the largest demand is coming from inside the industry.
“The biggest demand we see as a construction company is workforce and supply chain,” explained Justin. “Workforce is in high demand for all sectors of our industry. With supply chain challenges, extensive pre-planning and creativity in material selections are solutions that we, as a construction manager, have to provide insight on for our projects.”
Cheever Construction approaches each project with consistent objectives for success. They utilize an effective schedule coupled with the quality and skill from their subcontractors, combined with their field craftsmen. Their goal with each project is to make it the precursor to the “next” project, all while building a lasting relationship with everyone involved.
Invested in Success
Farris Engineering is an employee-owned building design firm that specializes in mechanical, electrical, plumbing, fire protection, and commissioning services. Their roots date back to 1967, and they’ve completed over 33,000 projects in more than 42 states.
Farris Engineering provides a broad swath of commercial building design and construction abilities. Everything from mechanical, plumbing, electrical, and data-comm design is part of every job. Farris Engineering ensures that all options and decisions are in step with what the client would like to see and needs for a successful project.
Farris is proud of the projects they have a hand in, and employees remember the time spent on each project fondly. Brad Kennedy, PE, LEED AP, shared with us some of his favorite projects that he has worked on with Farris.
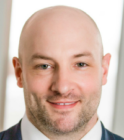
Brad Kennedy
Farris Engineering
“I enjoyed working on the Department of Defense and University of Nebraska projects. Our office has designed and helped build several buildings located in Minot, ND, Grand Forks, ND, as well as Whiteman Air Force Base in Missouri. These projects have ranged from simple office renovations to completely new hanger and maintenance facilities,” said Brad. “The larger, more recent project I was lucky enough to work on for the University of Nebraska was the East Campus – C.Y. Thompson Library renovation. The C.Y. Thompson library, now named the Dinsdale Family Learning Commons, was a major building transformation for the University of Nebraska East Campus.”
Brad also shared what has been popular in today’s market, along with why now is a great time to invest in Farris’ services.
“Following the pandemic, owners and clients are showing more concern about proper ventilation and on the flip side of that, energy conservation. Usually, these two points of design are hard to achieve together, but new energy recovery ventilators and controls are allowing increased ventilation and reduced energy consumption to be a reality,” Brad explained. “In today’s moving market, communication and sustainable decisions must come to the forefront of all construction projects. Energy will only become more expensive to the end user, so up-front discussions about how we can design a building that is not only life-cycle cost effective but safe, is top priority.”
With so many great local businesses available to help with your upcoming project, Farris wants to guarantee that their work sets them apart from the rest.
“I feel that Farris Engineering has the ability and experience to work in any type of building construction condition and usage. As I age in this industry, I feel that sustainability and energy conservation must be part of the grand picture for a project to be successful,” said Brad. “I also believe that communication between the owner, client, designers, and tradesman must be optimal to achieve a solid and functional building.”
Electrify Your Space
Every part of building construction is crucial to the overall project success and completion, and that includes what’s inside the walls, floors, and ceilings. Langer Electric is an excellent option for your electrical work. Owner Chris Langer has over 15 years of experience in the industry, and it’s important to him to help businesses strategize their energy needs and upgrades, with an eye toward increasing efficiency and reducing monthly electric bills for the long term. He keeps up with all codes and employee safety regulations to ensure that your building’s electrical system is truly safe and sound.
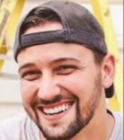
Chris Langer
Langer Electric
“Commercial construction offers tremendous opportunities for business owners, but it’s important to know all of the rules and opportunities,” Chris said. “As you plan your business space, Langer Electric can provide estimates for everything from fixture installation to panel updates, camera installation, repairs, maintenance, and pretty much anything electrical.”
Langer Electric has provided repair, maintenance, and installation services to commercial and residential clients, receiving an A+ rating from the Better Business Bureau. Chris strives to bring a level of comfort that feels as though you’re working with family, as well as a different level of customer satisfaction to the trade, which he says is hard to find these days. When performing electrical work for a commercial construction project, he believes preparation and communication are key to making the job successful.
“I make sure everything on my end is lined up with materials, labor, and communication between trades. We don’t EVER want to be the ones holding up a project,” Chris explained. “This includes establishing a relationship with inspectors for construction projects. My main concern with any project is making sure everything is completely in line with what the inspector wants. It doesn’t help anyone to butt heads with the one who ultimately calls the shots in the end. You have to be mindful of what exactly the inspector expects because each individual is different.”
Creating Intelligent Buildings
As the leading control technology contractor in Nebraska and Iowa, Engineered Controls offers a complete turnkey building-control solution, including system design, new construction, and owner-direct retrofit sales, installation, repair service, and preventive maintenance work for small buildings. Since 1994, they have been dedicated to designing easy-to-use building automation and security systems that provide the highest possible efficiency, all while ensuring occupant comfort and maintaining a safe and secure workplace. Their innovative and cost-effective building control solutions have been experienced by thousands of satisfied customers.
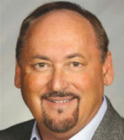
Pat Killeen
Engineered Controls
“We live in an era in which buildings of any size and shape can become intelligent buildings,” said Pat Killeen, president and CEO. “With open protocol technology, they can connect multiple subsystems together, on one network, rather than operating them all independently— maximizing energy efficiency, lowering maintenance costs, and providing centralized building control.”
It’s becoming more and more common for a building to have one central location to control all lighting, heating, cooling, and security functions, including outdoor controls and elevator controls. Not only is this incredibly convenient, but if you want your company’s building to go green, this is also an essential step.
“Our Energy and Environmental Optimization, or EEO, program certified professionals are equipped with the training, tools, and experience to quickly assess your building’s current state and consult with you on the goals and objectives of your energy efficiency project in detail,” explained Pat. “Our EEO professionals participate in a rigorous training program, in which they learn how to guide building owners and managers through a structured process of analysis and discovery. Leveraging the unique EEO toolset, they will partner with you to develop the right solution for your building.”
Engineered Controls’ EEO program software identifies poorly performing buildings and then provides and automates corrective actions. Their EEO certified professionals can help accelerate implementation of the most popular energy conservation measures to optimize your facility.
Improving the Bottom Line
Control Depot works hand-in-hand with Engineered Controls to provide them with the parts and products they need to carry out their work.
From their start in 2006, Control Depot has now progressed to being one of the leading Honeywell distributors in the nation. Honeywell is well-known throughout its 128-year history as a leader in temperature controls. As a twostep distribution channel, Control Depot is proud to offer the products and innovations that have made Honeywell a trusted partner in the industry.
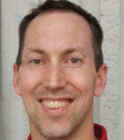
Jeff Killeen
Control Depot
“Control Depot’s primary goal is to offer the necessary systems and replacement parts that will provide a safe, comfortable working environment, as well as cut wasteful energy costs,” Vice President Jeff Killeen said. “We are helping companies become more sustainable and improve their bottom lines.”
As a Honeywell-Authorized Systems Distributor, Control Depot offers a full-line of Honeywell commercial and residential products to fulfill any HVAC controls or security needs. From a simple thermostat to a complex web-based building automation system, you can find it at Control Depot. In addition to wholesale counterline, Control Depot provides contractor programs, consulting services, parts coverage, control panel fabrication, training, and gas detection calibration.
“We have assembled a team of knowledgeable, qualified individuals whose goal is to assist each customer with personal service rooted in their experience. Because our inventory rivals any of the largest retailers, we can offer comprehensive solutions for building controls,” Jeff added. “Thanks to our partnership with Contemporary Controls, Control Depot offers additional technological solutions, which focus on providing reliable networking and communication for control systems.”
Businesses aren’t only considering indoor optimization to improve efficiency and comfort, many are also looking to their outdoor space for remodeling projects. Corporations such as Google and Microsoft have elected for outdoor spaces that allow their employees to work outside of the office or enjoy a leisurely view. From Facebook in the Silicon Valley to Shutterstock in New York City, spacious rooftop work spaces have become a popular choice even when outdoor space isn’t readily available. Businesses incorporating a pleasing outdoor space into their plans can create a welcoming environment for customers and attract young professionals to see them as a desirable employer.
Constructing a commercial building consists of critical details and decisions that can be made simple with the help of local experts. We encourage you to reach out to these Omaha professionals today to get started on building your next great project!